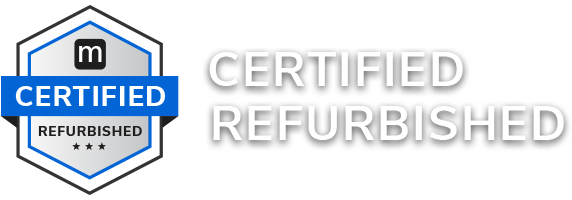
Each product goes through a thorough cleaning process. All prior data is securely erased, and a clean copy of the operating system is installed. Every product is then given a thorough external cleaning to ensure an accurate Visual Inspection as well as your satisfaction.
The Visual Inspection process involves a 40-point inspection. Our Certified Technicians inspect equipment for any cosmetic or operational issues. Issues are rare as equipment comes to us guaranteed operational from working environments. Our technicians also perform functionality tests (e.g. testing the hard drive, microphone, speakers, camera, etc.).
All equipment goes through a custom process conducting comprehensive hardware testing of:
In the rare instance equipment fails testing, a mac of all trades Certified Technician reviews the reported issue and performs the necessary repair. Some products with minor issues are sold in our clearance section. Only products with full functionality are listed in our standard product categories.
Equipment has passed all testing at this point. In the Repack stage, units are given a final visual inspection, packed, and labeled. Equipment is stored in our Finished Goods warehouse until sold.